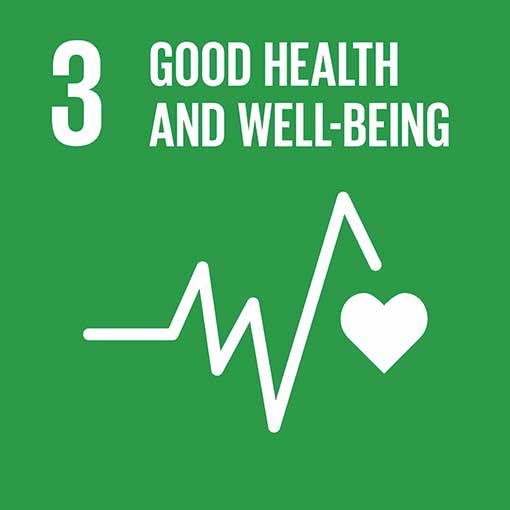
3.9 –By 2030, substantially reduce the number of deaths and illnesses from hazardous chemicals and air, water and soil pollution and contamination.
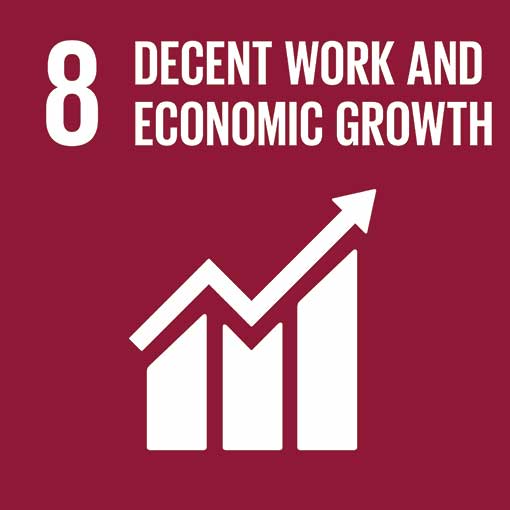
8.8 – Protect labour rights and promote safe and secure working environments for all workers, including migrant workers, in particular women migrants, and those in precarious employment
Protecting worker health and safety
Safety is a top priority at every Responsible Care company. For more than 34 years, CIAC members have been creating workplaces that are as healthy and safe as possible through initiatives such as the SHARE Network. Through this network, CIAC member company health and safety professionals work together to measure, track, and continuously improve performance, with the goal of achieving zero workplace injuries and illnesses.
Each year, CIAC collects Safety and Health Incident Metrics (SHIM) data. This data measures, tracks, and communicates health and safety trends to help member companies expand their efforts and extend their safety programs, further protecting the safety of everyone involved in the business of chemistry. Trends in the Total Recordable Incident Rate (TRIR) and Day Away from Work Incident Rate (DAWIR) for CIAC member employees and contractors between 2017-2021 are shown in Figure 16 and Figure 17.
Promoting process safety
To protect their workers, the public, and the environment, all CIAC member companies must have comprehensive process-safety management systems in place and adhere to standards established by the Canadian Society for Chemical Engineering. Any gaps between a company’s management system and the standards must be assessed, and action plans developed and implemented to raise the company’s process safety to an acceptable level. A comprehensive examination of a company’s process-safety management system is a fundamental component of the Responsible Care verification or audit process.
CIAC collects Process-Related Incident Measures (PRIM) data through an annual survey which has adopted the Center for Chemical Process Safety (CCPS) PRIM metrics. These metrics allow companies to track their own performance against industry process safety incident trends and identify opportunities for improvement.
Figure 18 shows some key insights from the annual PRIM survey. While the classification system for process safety events changed in 2016, Figure 18 does show that the number of Higher Learning Value (HLV– i.e., an event occurred but was of very low consequence or no actual event was recorded) events have increased over the last few years and overtaken both Tier 1 (loss of primary containment with the greatest consequence) and Tier 2 (loss of primary containment with lesser consequence) events.
What CIAC members are doing to promote safe and secure work environments
- Shell – Goal Zero initiative with Youth Wellness Hubs Ontario
- BASF – Psychological health and safety in the workplace
- Cabot Canada – Safety, health and environmental leadership award
- NOVA Chemicals – Training the next generation on critical safety and risk management
In 2022, the Shell Manufacturing Centre (SMC) highlighted the importance of safety by introducing a “Goal Zero” initiative for their Turnaround event (a scheduled event in which a refinery’s units are shut down, upgraded, and restarted) – setting aside a set amount of money for each incident-free day completed during the Turnaround.
The charity of choice for the 2022 Goal Zero initiative was Youth Wellness Hubs Ontario of Sarnia-Lambton, a new mental health and addictions centre for youth aged 11 to 25 and their families who are seeking low-barrier access to education, assessments, counselling, and treatment. Many core services (e.g., crisis counseling, housing, case management, and psychiatry) will be co-located in the new downtown Sarnia centre which is scheduled to open in 2023. This removes barriers to care, transforms the way service providers conduct their daily work, and improves care through a coordinated approach.
“This particular initiative is near and dear to my heart,” said Jason Woodward, Turnaround Event Manager. “My own family struggled to access services during the COVID-19 pandemic. SMC’s donation should support over 100 individual treatment cases.”
In 2022, BASF Canada completed a gap analysis of their Environmental, Health and Safety Management system against the CSA Z1003-Psychological Health and Safety in the Workplace Standard. Following the gap analysis, updates that have been made so far include an update to BASF Canada’s EHS Policy to include their commitment to employee psychological health and safety, development of a Psychological Health and Safety Committee (PHSC) that has 22 passionate and dedicated members across their Canadian organization, updates to their job postings and hiring practices to include psychological health and safety hazard recognition as a job responsibility for all roles and updates to their crisis management plan to include psychological support following different incidents.
Over the year, the PHSC has hosted eight different employee engagement webinars to discuss psychological safety awareness, coping mechanisms, and ending the stigma with their employees. Additionally, their Canadian Leadership Team was provided with Psychologically Safe Training During Challenging Times training, and 50 per cent of their people leaders in the organization participated in “How Managers Should Respond” training.
Cabot Canada Ltd. has been recognized for its outstanding performance in safety, health, and environmental leadership. The company was recently nominated for the award through their regional Chamber of Commerce and was selected as the winner.
The award recognizes Cabot Canada’s commitment to safety and environmental performance, which is evidenced by the company’s more than four years without a recordable injury and over 10 years without an environmental spill or release. “I was extremely proud to accept the award on behalf of the employees at Sarnia, just as I am proud of the effort our employees put in every single day in continuing our Drive to Zero,” said Dean Pearson, Facility General Manager of Cabot Canada Sarnia.
The company’s success in safety and environmental performance is due to the teamwork, communication, and effort put in by all employees and contractors to identify hazards and ensure that all workers can do their jobs safely.
Dean Pearson, Facility General Manager, Cabot Canada Sarnia accepting the Safety, Health and Environmental award
NOVA has had a 20-year partnership with the University of Alberta (U of A) to create programs for process safety and risk management. This partnership helps to support the industry’s commitment to sustainability and Responsible Care. NOVA employees, including Fred Henselwood, Sorin Dan, and Janeth Liendo, have worked with the U of A to create programs and guest lecture at process safety conferences and classes. Fred was recently awarded for his contributions to the U of A’s David and Joan Lynch School of Engineering Safety and Risk Management. NOVA’s commitment to Responsible Care remains strong, with a focus on Goal ZERO and ensuring safe and sustainable chemistry industry operations.