Product stewardship is a pillar of Responsible Care®. All CIAC member companies commit to taking responsibility for a product throughout its entire life cycle by reducing any environmental, health, or safety risks associated with it. Through this commitment, CIAC members are making progress on the following targets under UN SDG 12 (Responsible Consumption and Production):
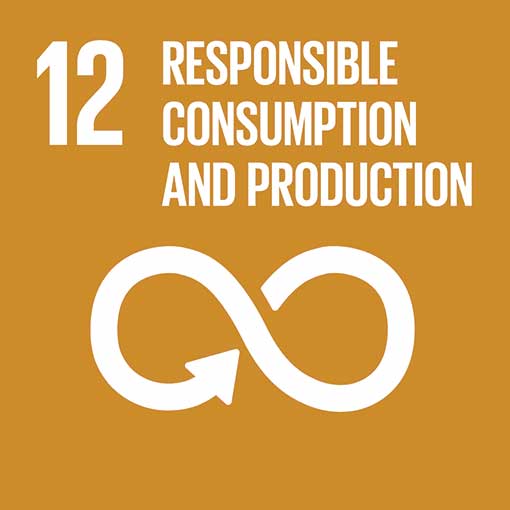
12.4 – By 2020, achieve the environmentally sound management of chemicals and all wastes throughout their life cycle, in accordance with agreed international frameworks, and significantly reduce their release to air, water and soil in order to minimize their adverse impacts on human health and the environment
12.5 – By 2030, substantially reduce waste generation through prevention, reduction, recycling and reuse
12.6 – Encourage companies, especially large and transnational companies, to adopt sustainable practices and to integrate sustainability information into their reporting cycle
Stewardship culture
Through Responsible Care, CIAC members are expected to instill a culture of stewardship throughout their organizations. CIAC considers stewardship a shared responsibility on behalf of all parties involved throughout the entire chemistry industry value chain. These parties are to share information to ensure the safe management of products throughout their life cycles. This requires the development of regular, sustained dialogue between member companies and their stakeholders, as well as working relationships between members, suppliers, customers, and any other relevant parties.
A culture of stewardship encourages all parties, regardless of their place along the value chain, to have in place active systems and processes that ensure the safe, environmentally sound, and socially responsible management of products. By taking the necessary steps to ensure that stewardship is exercised along the entire value chain, there is a much greater chance that the chemistry industry as a whole will meet the public’s increasing demand for safe, environmentally friendly, and sustainable chemistry products.
What CIAC members are doing to promote a culture of stewardship
- Dupont – A path to Positive Change
- Methanex – Handling methanol safely
- NOVA Chemicals – HDPE resins to advance a plastics circular economy
DuPont reformulated Styrofoam™ Brand XPS (extruded polystyrene) to reduce global warming potential (GWP) and advance DuPont’s 2030 Sustainability Goals.
To enhance their efforts to develop low-embodied carbon products, DuPont continuously evaluates the sustainability profiles of their innovation projects and apply LCA methodology to guide project decisions. DuPont’s Styrofoam™ Brand insulation products have played a critical role in improving energy efficiency in buildings for over 50 years. Styrofoam™ Brand XPS Insulation products are approximately 98 per cent gas and two per cent solid by volume, with the gas formula traditionally including hydrofluorocarbons (HFCs). Some HFCs have high GWPs and can contribute to climate change. DuPont innovation has enabled a viable, low-GWP solution to reduce the embodied carbon of Styrofoam™ Brand XPS Foam Insulation products while still delivering the same thermal performance, moisture resistance, durability, and ease of use expected by customers. Converting to the low GWP Styrofoam™ Brand XPS Insulation results in a substantial 94 per cent reduction in carbon footprint for this product line. In support of this innovation, DuPont launched the beyondblue.dupont.com website, which highlights our GWP phase-down program and shares product transparency documentation for these products.
Appropriate safety precautions must be taken when using, handling, or working around methanol to keep people and the environment safe. Through its product stewardship program, product safety practices, and participation in industry associations across regions, Methanex provides information on managing the risks of methanol and promotes its proper use and safe handling.
In 2022, Methanex hosted 30 safety webinars and seminars that reached more than 900 people from 193 organizations. The attendees included supply-chain partners, customers, terminals, surveyors, distributors, carriers, and emergency services, as well as local and regional authorities in all the regions where the company has sales activities. The company believes that educating all stakeholders on safe handling practices is crucial in ensuring the safety of people and the environment.
In June 2022, NOVA Chemicals introduced a new resin technology for machine direction oriented (MDO) and biaxially oriented (BO) processes to help its customers and brand owners meet their sustainability goals. NOVA Chemicals’ innovative technology marks a major advancement in the pursuit of the plastics circular economy as it enables recyclable all-polyethylene (PE) packaging.
Oriented film structures allow easy-to-recycle all-PE packaging to replace traditionally non-recyclable mixed material packaging. In addition, orientation of PE films allows for property improvements otherwise not attainable in blown or cast films such as enhanced stiffness, toughness, and optical properties. Oriented films are ideal for use in food packaging, heavy duty shipping sacks, e-commerce and other demanding applications and being able to produce HDPE-based oriented films is a significant step towards industry’s goal of 100 per cent recyclable packaging.